“Shini Products” in the Toy Industry
As the world's largest toy exporter, China produces nearly 75% of the world's toys. Behind this mighty world factory, there are hundreds and thousands of toy production lines. For the fierce competition behind the production line, how to stand out among many competitors and be among the best is the problem facing each enterprise.
Simeijia is an important partner of Shini. In recent years, it has emerged in the toy market with continuously bursting-out energies. Therefore, let's go into Simeijia and find out how Shini system products helped it to develop.
Besides the feeding problem, there are many problems, such as excessive workers, inefficiency, dust, and too much noise in the workshop of Simeijia. Facing these tricky and challenging problems, it turns to Shini for the solution.
The background of customer demands
Simeijia has 112 sets of auto high-performance electric injection molding machines, with a total material consumption of about 1.2t/hr. The maximum horizontal and vertical distances of the material conveying are 135m and 3.5m, respectively.
Shini Solutions
Relying on the smart injection molding plant, Shini integrates the central feeding system, dehumidification and drying, color dosers, and other systems and equipment and reserves the future expansibility for the digitalized plant. Which lays all pipelines overhead to make the tidy equipment and simple layout, help customers improve all-round production efficiency and workshop environment, and solve the production problems. Materials discharged from the material storage tank are pumped to Shini silo through Shini Vacuum Hopper Loader and then distributed to the large dryers through the pipeline for dehumidifying and drying. The end-to-end integration forms mature technology from the material to the input and product output, thus improving the automation degree of the material, conveying and consolidating the digital basis.
Simeijia uses 112 sets of machines in the production, so Shini plans four central control stations according to the regional, which is convenient for the machine classification and control in different regions.
In terms of material distribution, Shini uses the material distribution station SMDS to distribute the corresponding material storage tank, and it equips the quick connectors for easy loading and unloading; All parts are made of stainless steel for no contamination; The instant materials are conveyed into the stainless steel pipe through each hose, and then discharged into each machine through the hose. As the materials are mixed with dust, the central filter is a virtual machine in the system application. Its filtering accuracy reaches 5 microns, which can effectively filter the dust. The cloth bag and support can be quickly removed and replaced; Equipped with an air accumulator and auto purging device, it can automatically clean the dust on the cloth bag and reduce the frequency of manual cleaning.
As each group of machines produces different building blocks, each machine is equipped with Shini color dosers. The primary material is stored in the main hopper. The masterbatch and recycled materials are stored with the doser hopper on top of the screw. Thus making the virgin materials, recycled materials, and masterbatch work together. In addition, Shini Low-speed Granulator is placed beside each machine for instant sprues' recycling. Through the close cooperation of the above two contestants, the building blocks produced are finally made into a set of beautiful building block toys through an intelligent warehouse system and manual assembly and packaging sold worldwide.
It took us only three months to deploy the Shini Central Conveying System project. It has been officially put into operation for over one year now, which customers have highly praised in early planning, production, quality, and after service.
In the future, Shini will continue to provide even more high-quality system products, solutions, and services, and maintain and develop an excellent cooperative relationship with customers to realize the mutual benefit, win-win and shared prosperity with the customers.
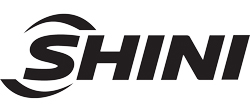
SHINI Official Website:
http://www.shini.com
SHINI at PRM-TAIWAN:
https://www.prm-taiwan.com/com/shini.html
Simeijia is an important partner of Shini. In recent years, it has emerged in the toy market with continuously bursting-out energies. Therefore, let's go into Simeijia and find out how Shini system products helped it to develop.
Besides the feeding problem, there are many problems, such as excessive workers, inefficiency, dust, and too much noise in the workshop of Simeijia. Facing these tricky and challenging problems, it turns to Shini for the solution.
The background of customer demands
Simeijia has 112 sets of auto high-performance electric injection molding machines, with a total material consumption of about 1.2t/hr. The maximum horizontal and vertical distances of the material conveying are 135m and 3.5m, respectively.
Shini Solutions
Relying on the smart injection molding plant, Shini integrates the central feeding system, dehumidification and drying, color dosers, and other systems and equipment and reserves the future expansibility for the digitalized plant. Which lays all pipelines overhead to make the tidy equipment and simple layout, help customers improve all-round production efficiency and workshop environment, and solve the production problems. Materials discharged from the material storage tank are pumped to Shini silo through Shini Vacuum Hopper Loader and then distributed to the large dryers through the pipeline for dehumidifying and drying. The end-to-end integration forms mature technology from the material to the input and product output, thus improving the automation degree of the material, conveying and consolidating the digital basis.
Simeijia uses 112 sets of machines in the production, so Shini plans four central control stations according to the regional, which is convenient for the machine classification and control in different regions.
In terms of material distribution, Shini uses the material distribution station SMDS to distribute the corresponding material storage tank, and it equips the quick connectors for easy loading and unloading; All parts are made of stainless steel for no contamination; The instant materials are conveyed into the stainless steel pipe through each hose, and then discharged into each machine through the hose. As the materials are mixed with dust, the central filter is a virtual machine in the system application. Its filtering accuracy reaches 5 microns, which can effectively filter the dust. The cloth bag and support can be quickly removed and replaced; Equipped with an air accumulator and auto purging device, it can automatically clean the dust on the cloth bag and reduce the frequency of manual cleaning.
As each group of machines produces different building blocks, each machine is equipped with Shini color dosers. The primary material is stored in the main hopper. The masterbatch and recycled materials are stored with the doser hopper on top of the screw. Thus making the virgin materials, recycled materials, and masterbatch work together. In addition, Shini Low-speed Granulator is placed beside each machine for instant sprues' recycling. Through the close cooperation of the above two contestants, the building blocks produced are finally made into a set of beautiful building block toys through an intelligent warehouse system and manual assembly and packaging sold worldwide.
It took us only three months to deploy the Shini Central Conveying System project. It has been officially put into operation for over one year now, which customers have highly praised in early planning, production, quality, and after service.
In the future, Shini will continue to provide even more high-quality system products, solutions, and services, and maintain and develop an excellent cooperative relationship with customers to realize the mutual benefit, win-win and shared prosperity with the customers.
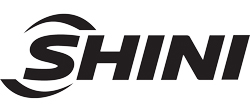
SHINI Official Website:
http://www.shini.com
SHINI at PRM-TAIWAN:
https://www.prm-taiwan.com/com/shini.html
E-News Categories
Экструдеры и экструзионные линии
- Экструзионная линия для пневматической пузырьковой пленки
- Экструзионная линия для пневматической пузырьковой пленки
- Линия для совместной экструзии с воздушным пузырьком
- Машины для изготовления пакетов
- Машина для производства пенопласта
- Выдувание пленки
- Машина для производства выдувных пленок
- Литьевая машина
- Покрывающая машина
- Экструзионная линия для пенопласта EPS / EPE
- Экструдер
- Ламинирующие машины
- Extrusion Lines For Filaments and Yarn
- Extrusion Lines For Pipes and Profiles
- Экструзионная техника для моноволокна
- Экструзионная линия для моноволокна
- PET Strapping Band Extrusion Lines
- Машины для изготовления пластиковых пакетов
- Совместная экструзия пластмассовой пленки
- Машины для производства пластиковых труб
- Машина для изготовления пластиковых труб
- Машина для производства ПВХ-шлангов
- Машины для производства соломы
- Двухшнековый экструдер
- Двухшнековые экструдеры
- Машина для производства тканого мешка
Перерабатывающее оборудование для предварительной обработки
- Линия для мытья бутылок
- Дробилка
- гранулятор
- гранулятор
- Грануляторы
- Pelletizing Machines
- Линия рециркуляции ПЭТ-бутылок
- Плита горячего мытья
- Машина для гранулирования
- Оборудование для переработки пластмасс для предварительной обработки
- Машины для переработки пластика
- Машина для переработки пластиковых отходов
- Перерабатывающие линии
- Машина для переработки отходов
- бумагорезка
- соковыжималки
- Бельевая веревка
- Оборудование для переработки отходов